TOUR THROUGH THE MANUFACTORY DEUMER
Deumer has been pioneering the development of cufflinks and other small accessories since 1863. With many trendsetting innovations, for example the adoption of electrolysis bath gilding, vitreous enameling or the fixed link as variation of the until than common chain link. For over a century, people all over the world have been accompanied by cufflinks, money clips and other accessories from this owner-managed family business, now in its 6th generation.
A MANUFACTURER'S CREED 1926
„It has always been the aspiration of my manufactory, to only deliver quality goods, and I endeavor, to still continuously raise the quality. Some now offer sub par goods at a low prices. I will never let this divert me from my way, as quality goods will always assert itself. Those who aspire to put in honor with their delivery and to secure their customers for repeat business, will always choose the best of the good. Quality product is the cheapest, and only it enables smooth and continuous business.“
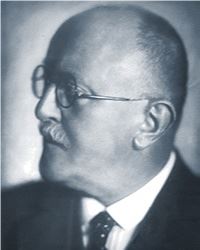

With the engravers
Production starts in the hands of the engraver, with the creation of the embossing tool. He is both craftsman and artist. He incises the desired image into the steel and thus lays the foundation. Deumer has had the good fortune to train, employ and work with Germany’s best engravers. Deumer's most famous engraver was Wilhelm Jüngermann, teacher, illustrator, medallist and sculptor who became famous far over the borders of his home town Lüdenscheid.
Into the mint
At the mint, the cufflink is given his form and motif. After the embossing tool is hardened, a blank is cut from silver or gold in the right strength, manually and piece by piece put into the mint and then minted once, twice or three times, with up to 800T of pressure. Care and specific knowledge towards the setting and use of the machines is pivotal to not damage the embossing tool and thus the engravers work as well as to ensure a repeatable result in high serial quality. After minting, the blank is deburred and receives its finished shape.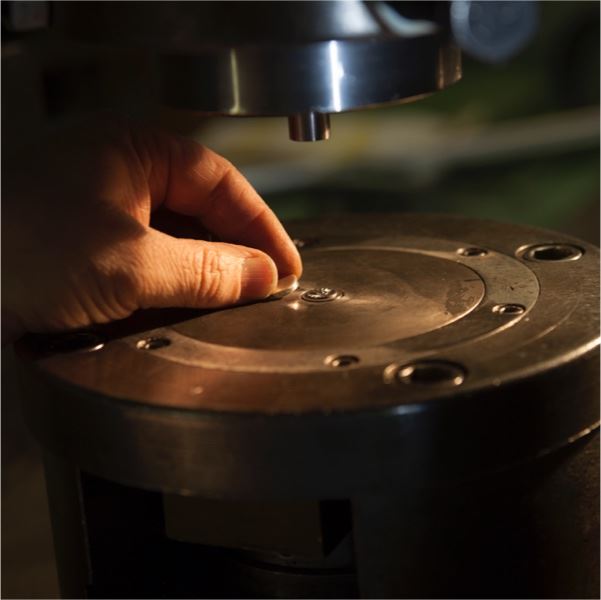
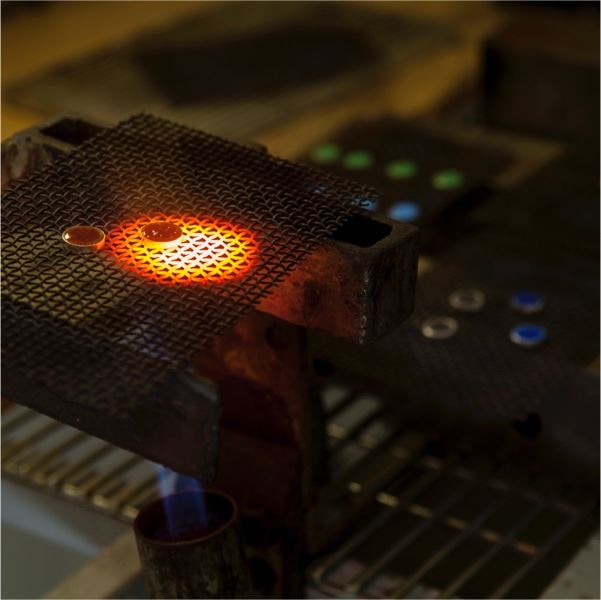
In the enameling shop
Deumer is Germany's only manufactory, that still commands and offers this 3500 years old art today. For the cloisonné or champlevé enameling technique the final motif is embossed in the form of several depressions each divided by thin strips. For every color of the image, the depressions are filled separately with powdered vitreous enamel mixed in a special liquid, dried, fired, cut, fired again and finally polished. For the “émail en basse taille”-technique, a motif is engraved below the uniform colored transparent enameling.MANUFACTORY TODAY
Manufactories are not per se better, but simply a special, not so far spread from of production. It is above all not fit for large scale production. Manufactories unite the art of craftsmanship with the industrial division of labour. Today manufactories stand for a new form of exclusiveness. For handmade and bespoke goods of outstandingly high quality and value. Authenticity and individuality of manufactory-goods, transparency of the manufacturing process and the materials used are the most important characteristics.In the brazing shop
At the brazing shop single parts are fitted to become one whole. Brazing connects front and back of the cufflink via a fixed bar. Deumer uses an especially elaborate method of hard soldering. That means, that the material of every single part is heated until they almost reach their melting point and are then fitted together. This creates a uniform non-detachable Connection. An especially challenging is the hard soldering of enameled parts. The danger is great that the colors burn in the process, change during the cooling or crack due to the different materials different surface tensions.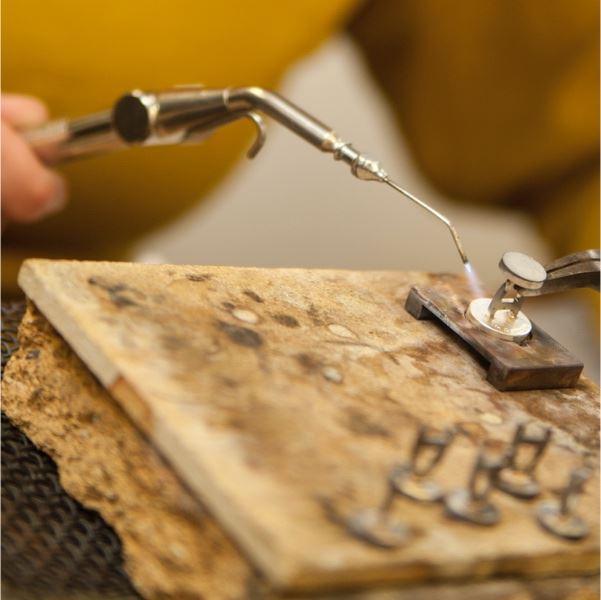
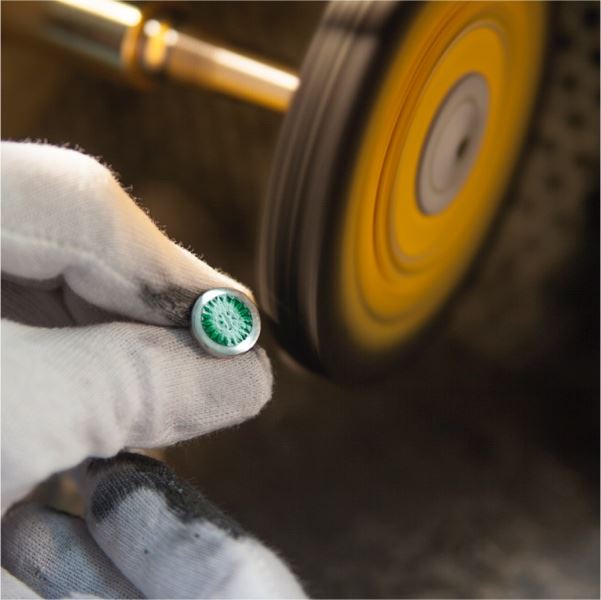
In the polishing workshops
A manufactory requires strong hands: In the polishing shops. This department of the manufactory gives every product its final surface structure. All remaining edges or grates are cut down, all surfaces are either completely or partly matted and polished. Especially the polishing requires a lot of strength, practice and care in order to even out even the smallest irregularities. Polishing is still done by hand, with a polishing block, a plurality of polishing wheels from different materials and even more different kinds of polish.ARE MANUFACTORIES STILL UP TO DATE?
Yes, manufactories are up to date. They are an important part of the discussions on work-life balance. Being able to create something beautiful with ones own hands makes work once more meaningful and an experience. Goods created in a manufactory are long-lived and that alone makes them part of a sustainable economy. The perfect handcraft, the high quality and timeless elegance of manufactured goods are the modern man’s alternative to an all-banalizing mass consumption.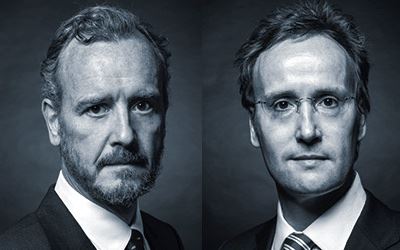
The electroplating shop
The electroplating shop is one of the core pieces of Deumer Manufactory. Here, every single product receives its final precious metal coating to give it its surface color. This craft too, requires a specialist, a thorough training and years of experience, not in the least to ensure that all environmental regulations concerning the acids and bases involved are complied with. Deumer invests in state of the art technologies to ensure that it fulfills its responsibilities towards the environment and to ensure a sustainable manufacturing process. The coatings contain a on a nano basis developed a corrosion protection to minimize tarnishing.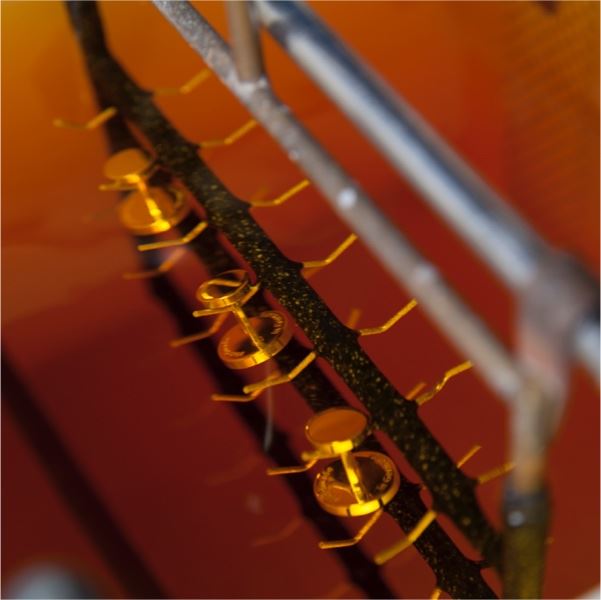
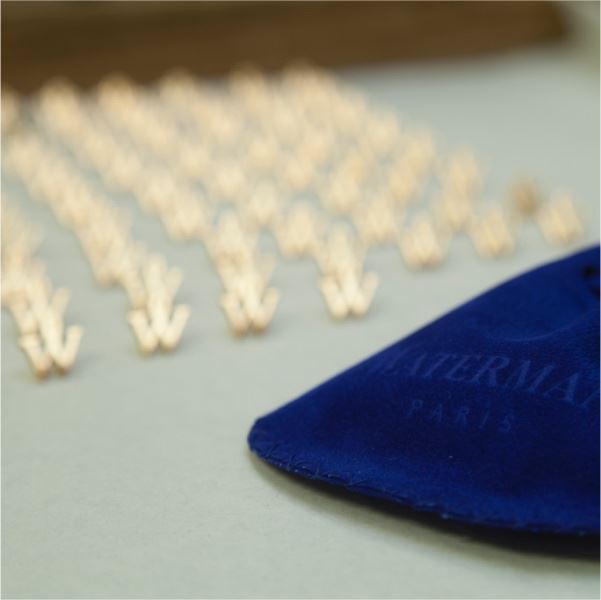